Mehanizam razgradnje kovanja plijesni
Kovanje pod tlakom trenutno je najnaprednija tehnologija kovanja, uglavnom se koristi za masovnu proizvodnju ključnih komponenti kalupa. Najveći nedostatak je loša izdržljivost alata za oblikovanje. Prema uredniku diecastingcompany.com, cijena alata iznosi 8-15% ukupne cijene proizvoda. Zapravo, ako uzmete u obzir vrijeme potrebno za zamjenu istrošenog alata i gubitak uzrokovan slučajnim kvarom, troškovi mogu iznositi čak 30% do 50%. Štoviše, trošenje alata uzrokovat će značajno pogoršanje kvalitete kovanja. Najčešći nedostaci uzrokovani trošenjem alata su greške pri punjenju šupljine, odnosno presavijanje, neravnine, deformacije, ogrebotine, delaminacija i mikro i makro pukotine.
Ovi nedostaci će na kraju utjecati na performanse krivotvorenih proizvoda. Zbog jake konkurencije na tržištu, proizvođači proizvoda za kovanje nastavljaju smanjivati svoje troškove uz poboljšanje kvalitete otkivaka. Uprkos tome, i dalje su jako zainteresirani za problem slabe trajnosti alata.
Trajnost alata obično se definira na nekoliko načina. U proizvodnom smislu, trajnost alata izražena je brojem otkovaka, odnosno brojem proizvoda očekivane kvalitete koji se mogu dobiti ovim alatom. Prema ovoj definiciji, prosječna trajnost alata može varirati između 2,000 i 20,000 komada. Što se tiče alata, trajnost je povezana s degradacijom, pa se definira kao sposobnost izdržavanja fenomena degradacije. Ovaj članak uglavnom koristi drugu definiciju. Treba reći da na alate za kovanje utječu različiti degradirajući faktori tijekom upotrebe, a interakcija ovih faktora otežava analizu problema. U literaturi o ovoj temi mogu se pronaći različita objašnjenja fenomena degradacije.
Prema statistikama mnogih naučnika, glavni razlog povlačenja kovačkih kalupa iz upotrebe su promjene u dimenzijama habanja. Otpad plijesni zbog trošenja čini oko 70%, plastične deformacije čine oko 25%, a zamorno pucanje i drugi razlozi čine samo oko 5%. Mnogi se fenomeni često događaju istovremeno, a njihova interakcija ovisi o dizajnu kalupa, uvjetima njihovog kovanja i proizvodnje, toplinskoj obradi materijala za kalup te obliku predforme i umetka.
Radni uslovi kovanja: U procesu toplog kovanja alati su uglavnom izloženi degradaciji sa tri aspekta: intenzivnog toplotnog udara, periodičnih promena mehaničkog opterećenja i visoke temperature i visokog pritiska. Kako bi se smanjilo napon tečenja čeličnih proizvoda tijekom vrućeg kovanja, deformirani metal zagrijava se na 10,000-2,000 stupnjeva Celzijusa. U trenutku deformacije materijala temperatura površine alata može doseći 800 stupnjeva Celzijusa, nakon čega slijedi intenzivno hlađenje, pa će stoga alat biti izložen velikom temperaturnom gradijentu. Na presjeku kalupa, temperatura površine kalupa i temperatura pri površini mogu se razlikovati za nekoliko stotina stepeni Celzijusa. Temperatura vrućeg kovanja niža je od temperature vrućeg kovanja, odnosno temperatura deformacije čelika doseže oko 900 stepeni Celzijusa. To znači da opterećenje koje nastaje cikličnim zagrijavanjem i hlađenjem površine alata nije toliko veliko kao vruće kovanje. Ipak, vijek trajanja alata koji se koriste u procesu polugrijanog kovanja i dalje je vrlo kratak. To je uglavnom zbog kombiniranog učinka ciklične temperature i većeg mehaničkog opterećenja. Mehaničko opterećenje uglavnom dolazi od hlađenja i tvrđih materijala.
Mehanizam degeneracije alata za kovanje
Vijek trajanja alata za kovanje uglavnom ovisi o njihovom dizajnu, pripremi, toplinskoj obradi materijala alata, uvjetima kovanja, obliku predformi i jezgri, itd. U literaturi o ovoj temi možemo pronaći mnogo podataka o degradaciji. Ovi mehanizmi su podijeljeni u različite kategorije. Rezultati istraživanja pokazuju da se na površini alata za kovanje uglavnom pojavljuju sljedeći mehanizmi habanja: abrazivno trošenje, termomehanički zamor, plastična deformacija, pucanje uslijed zamora, trošenje ljepila i oksidacija. Oblik radnog udubljenja alata određuje vrijeme kontakta, pritisak, put trenja i promjene temperature, što određuje brzinu pojave posebnog mehanizma razgradnje.
U ravnom području vrijeme kontakta između alata i termičkog materijala je najduže, a ujedno je i mjesto gdje dolazi do maksimalnog pritiska. Termomehanički zamor je glavni mehanizam razgradnje.
Na unutarnji radijus zaobljenja utječe ciklično vlačno opterećenje, uzrokovano povećanjem vanjskog opterećenja, koje se uglavnom događa kada se deformacija nastoji koncentrirati tijekom procesa kovanja. Kao rezultat toga, mikropukotine zamora se razvijaju u velike pukotine tijekom servisa alata i pojavljuju se na tim mjestima. Vanjski radijus udubljenja kalupa i mjesto gdje otisak kalupa ulazi u fleš most zbog slabljenja materijala pod visokim temperaturama, niža je granica tečenja materijala, što dovodi do plastične deformacije. Gust tok deformiranih materijala uzrokuje abrazivno trošenje u tim područjima, što dodatno pogoršavaju tvrdi oksidi, koji nastaju na površini materijala za kovanje alata tijekom procesa oksidacije na visokim temperaturama.
Adhezivno trošenje mehanizma razgradnje kovačkih matrica
Ljepilo se troši u području plastične deformacije površinskog sloja, posebno tamo gdje je površina nepravilna. Obično se javlja pod visokim pritiskom i relativno malom brzinom, uglavnom zbog sličnih interakcija materijala ili materijala koji pokazuju kemijski afinitet (tipični uvjeti obrade kovanja). Pod uvjetima višeg tlaka, oblikovanje materijala klizi po površini alata, uklanjajući oksidni premaz, ostavljajući svježu površinu alata izloženom. To se uglavnom događa u nepravilnom području površinske projekcije (vršni dio hrapave površine).
Kada se materijali na tim mjestima postave jedan blizu drugog, tako da međuatomske sile počnu djelovati, stvaraju se lokalne metalne veze. Zatim, kako su se površine pomjerile jedna prema drugoj, metalna veza je uništena. U tom procesu nastaje plastična deformacija površinskog sloja. Pucanje metalne veze dovodi do ljuštenja metalnih čestica koje se teže lijepiti za površinu.
Abrazivno trošenje mehanizma razgradnje kovačkih matrica
Gubitak materijala obično se pripisuje abrazivnom trošenju. Veličina oljuštenih čestica uglavnom ovisi o koeficijentu kovanja i svojstvima površinskog sloja alata. Primjer trošenja ljepila je druga faza kovanja kućišta CV univerzalnog zgloba, kako je prikazano na slici. Temperatura na kojoj se materijal deformira u ovom procesu je oko 900 ° C, odnosno obično je znatno niža od tradicionalnog procesa vrućeg kovanja, koji je obično ova vrsta trošenja. Ljepilo će se zalijepiti za sam materijal ili za alat, gdje se smanjuje površina poprečnog presjeka.
Abrazivno trošenje je rezultat gubitka materijala i uglavnom se postiže odvajanjem materijala od površine. Abrazivno trošenje će se pojaviti kada postoje labave ili fiksirane abrazivne čestice, ili kada postoje nepravilni dijelovi izbočina na interakcijskoj površini. Za alat za kovanje njegova tvrdoća je mnogo veća od tvrdoće deformiranog materijala. U tom slučaju, ako se abrazivne čestice pojave u kontaktnom dijelu između alata za kovanje i deformiranog materijala, doći će do abrazivnog trošenja. Abrazivno trošenje pogoršat će se pojavom čestica tvrdog oksida, koje nastaju na površini malih čestica odvojenih od dijela za kovanje, kalupa i površine kalupa pod visokim temperaturama. Zahvaljujući ovom mehanizmu, u smjeru u kojem se mijenja deformacija materijala stvaraju se utori.
Njihov oblik i dubina uglavnom ovise o uvjetima kovanja. Izbačeni dio posebno je osjetljiv na habanje i brzo će se ukloniti s površine alata tijekom daljnjeg servisiranja, što dovodi do gubitka materijala i promjene u geometriji materijala. Posebno lako nastaje abrazivno trošenje, a posebno je osjetljivo na abrazivno trošenje mjesto na kojem dolazi do najdužeg klizanja tijekom deformacije materijala. Najčešći je vanjski radijus šupljine kalupa, gdje kalup ulazi u fleš most.
Molimo zadržite izvor i adresu ovog članka radi ponovnog štampanja: Mehanizam razgradnje kovanja plijesni
Minghe Tvrtka za lijevanje tla posvećeni su proizvodnji i pružaju kvalitetne dijelove i dijelove za lijevanje visokih performansi (opseg dijelova za livenje metala uglavnom uključuje Tankozidno lijevanje,Vruće komore Die Casting,Livenje u hladnoj komori), Okrugla usluga (usluga lijevanja,CNC obrada,Izrada kalupa, Površinska obrada). Bilo koji prilagođeni lijev od aluminija, livenje magnezijumom ili Zamakom / cinkom i drugi odljevci dobrodošli su da nas kontaktirate.
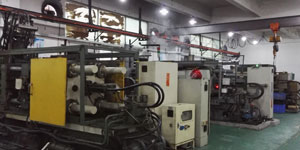
Pod kontrolom ISO9001 i TS 16949, svi procesi se provode kroz stotine naprednih mašina za livenje pod tlakom, 5-osnih mašina i drugih objekata, od blastera do Ultra Sonic mašina za pranje rublja. Minghe ne samo da ima naprednu opremu već ima i profesionalnu opremu tim iskusnih inženjera, rukovatelja i inspektora kako bi ostvarili dizajn kupca.
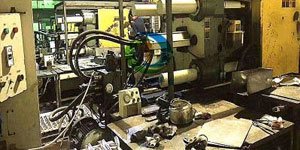
Ugovorni proizvođač kalupa. Mogućnosti uključuju dijelove za livenje aluminijuma u hladnoj komori od 0.15 lbs. do 6 lbs., brza promjena i obrada. Usluge s dodanom vrijednošću uključuju poliranje, vibriranje, uklanjanje brušenja, miniranje sačmama, farbanje, oblaganje, premazivanje, montaža i obrada alata. Materijali s kojima se radi uključuju legure poput 360, 380, 383 i 413.
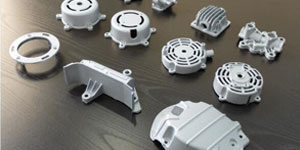
Pomoć pri dizajniranju lijevanja cinkom / istovremene inženjerske usluge. Prilagođeni proizvođač preciznih odljevaka od cinka. Mogu se proizvoditi minijaturni odljevci, odljevci za kalupe pod visokim pritiskom, odlivci kalupa sa više klizača, konvencionalni odljevci od kalupa, odljevci za kalupe i neovisni kalupi i odljevci sa šupljinom. Odljevci se mogu izrađivati u dužinama i širinama do 24 in. U toleranciji +/- 0.0005 in.
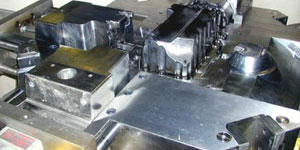
ISO 9001: 2015 certificirani proizvođač lijevanog magnezijuma. Mogućnosti uključuju lijevanje magnezijumom pod visokim pritiskom do 200 tona vruće komore i 3000 tona hladne komore, dizajn alata, poliranje, oblikovanje, obrada, farbanje u prahu i tečnostima, puni QA sa CMM mogućnostima , montaža, pakovanje i dostava.
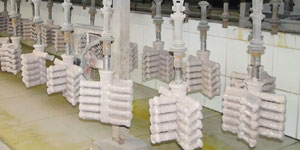
Ovjeren ITAF16949 Dodatna usluga lijevanja uključuje investiranje,livenje peska,Gravitacijsko lijevanje, Casting Lost Foam,Centrifugalno livenje,Vakuumski livenje,Trajno lijevanje kalupa, .Sposobnosti uključuju EDI, inženjersku pomoć, solidno modeliranje i sekundarnu obradu.
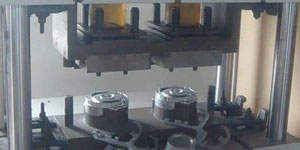
Casting Industries Studije slučaja za dijelove za automobile, bicikle, zrakoplove, muzičke instrumente, plovila, optičke uređaje, senzore, modele, elektroničke uređaje, kućišta, satove, mašine, motore, namještaj, nakit, vrpce, telekom, osvjetljenje, medicinske uređaje, fotografske uređaje, Roboti, skulpture, zvučna oprema, sportska oprema, alat, igračke i još mnogo toga.
Šta vam možemo dalje pomoći?
∇ Idite na početnu stranicu za Kina za lijevanje pod pritiskom
→Dijelovi za lijevanje- Otkrij šta smo uradili.
→ Povezani savjeti o Usluge lijevanja
By Proizvođač lijevanja Minghe | Kategorije: Korisni članci |materijal Tagovi: Aluminijsko livenje, Lijevanje cinka, Magnezijum lijevanje, Titanijsko livenje, Lijevanje nehrđajućeg čelika, Lijevanje od mesinga,Lijevanje bronce,Casting Video,Istorija kompanije,Aluminijsko livenje | Komentari isključeni