Kontrola procesa proizvodnje vermikularnog željeza
U usporedbi sa sivim željezom, vlačna čvrstoća vermikularnog željeza povećava se za najmanje 70%, modul elastičnosti se povećava za 35%, a čvrstoća na zamor se gotovo udvostručuje. U usporedbi s aluminijskom legurom, čvrstoća i krutost vermikularnog željeza dvostruko su veće, a čvrstoća na zamor dva puta veća. Ove karakteristike vermikularnog željeza pružaju mogućnost motoru da poboljša omjer snage i težine i poveća pritisak u cilindru. Povećanje tlaka u cilindru ključ je za optimalne performanse sljedeće generacije dizelskih motora s direktnim ubrizgavanjem. Kako bi zadovoljila široku primjenu vermikularnog željeza, ljevaonica se trenutno aktivno priprema, ulaže velika sredstva i obnavlja nove procese kako bi proizvodnju vermikularnog željeza učinila stabilnom i pouzdanom.
Za vermikularne željezne motore, od prototipa do masovne proizvodnje, odlučujući faktor je rizik kvalitete. Za visokokvalitetno vermikularno željezo, stabilna zona je vrlo mala, samo u rasponu od 0.008% sadržaja magnezija. Količina u tragovima, poput gubitka 0.001% magnezija, proizvest će ljuskasti grafit, što će uzrokovati pad mehaničkih svojstava za 25% do 40%. Ovaj članak opisuje sistem upravljanja procesima zasnovan na metodama termičke analize. Sistem mjeri gubitak magnezija i prilagođava stanje rastopljenog željeza na mreži kako bi spriječio stvaranje ljuskastog grafita. Ova internetska kontrolna metoda mjerenja i podešavanja smanjuje hlapljivost u procesu proizvodnje vermikularnog željeza do najniže tačke i u osnovi eliminira rizik kvalitete uzrokovan proizvodnjom vermikularnog željeza.
Potražnja za visokim konjskim snagama, velikim okretnim momentom, niskim emisijama ispušnih plinova i smanjenom potrošnjom goriva nastavlja rasti. To prisiljava dizajnere dizel motora velike snage da povećaju vršni pritisak paljenja, što uvelike povećava toplinsko opterećenje i mehaničko opterećenje motora. Toplinsko i mehaničko opterećenje istovremeno se povećavaju, tako da su konvencionalni motori od lijevanog željeza i lijevanog željeza (CrMo) koji se trenutno koriste dostigli ili premašili gornju granicu svoje upotrebe. Proizvođačima motora potrebni su materijali veće čvrstoće i bolje otpornosti na toplinu.
Vermikularno željezo brzo je postalo materijal izbora ljudi. To uvelike poboljšava pouzdanost bloka cilindra, glave motora i košuljice cilindra nove generacije motora kamiona. Da bi se postigla najbolja kombinacija različitih svojstava (kao što su svojstva lijevanja, svojstva obrade, toplinska vodljivost i mehanička svojstva), ovi dijelovi moraju biti izrađeni sa stopom sferoidizacije od 0% do 20% (stopa puzanja od 80% do 100% ) Od vermikularnog gvožđa. Ako stopa sferoidizacije prelazi 20%, uzrokovat će niz nepovoljnih čimbenika. Na primjer, količina skupljanja je prevelika, a dijelovi složenih oblika, poput glava cilindra, posebno su skloni skupljanju. Drugi primjer je smanjenje vijeka trajanja alata zbog prekomjernog trošenja tijekom obrade. Postoji i značajno smanjenje toplinske vodljivosti, uzrokujući toplinski stres i tako dalje. Na drugom kraju vermikularnog željeza, pojavljivanje ljuskastog grafita uzrokovat će linearno smanjenje mehaničkih svojstava, čineći motor nesposobnim ispuniti nove zahtjeve. Ukratko, kako bi se zadovoljile potrebe nove generacije kamionskih motora, stopa sferoidizacije vermikularnog željeza velike čvrstoće mora biti između 0% i 20% (to jest, stopa puzanja je iznad 80%, bez pahuljica).
Hoće li se koristiti kontrola proizvodnog procesa ili ne, ovisi o godišnjoj proizvodnji proizvoda, složenosti proizvoda i dopuštenom rasponu promjena u metalografskoj strukturi. Kao što je prikazano na slici 1, relativno jednostavni dijelovi male zapremine, poput kalupa za ingote, općenito se mogu proizvesti konvencionalnim metodama lijevanja. Kontrola procesa općenito nije potrebna i nije ekonomski isplativa. Kada se godišnja proizvodnja komponenti poveća, kao što su ispušne cijevi, radilice i držači, trebalo bi imati smisla uvesti kontrolu procesa. Iako ova vrsta proizvoda ima veliku godišnju proizvodnju, godišnja tonaža lijevanja nije velika. Zahtjevi metalografske strukture nisu vrlo strogi, pa dopuštaju da stopa sferoidizacije bude čak 50%. Osim toga, zbog male količine obrade takvih dijelova, povećanju titana koji se može dodati u proizvodnji može se omogućiti proširenje raspona koji se može kontrolirati. Za ovu vrstu proizvoda uobičajene metode lijevanja i stroga obuka općenito su mjerodavni za proizvodnju vermikularnog željeza. Ali iz perspektive kontrole kvaliteta, kontrola procesa bi trebala biti sigurnija. Slično, kontrola procesa također daje garanciju za proizvodnju velikih brodskih blokova motora i glava cilindara. Iako velike veličine i mala količina proizvodnje pogoduju proizvodnji proizvoda, ekonomski gubici uzrokovani proizvodima koji prelaze standard dovoljni su za dodavanje skupa sistema za kontrolu procesa.
Proizvodi kojima je najpotrebnija kontrola procesa su blokovi cilindara motora motora, glave cilindra i kočioni diskovi s velikom godišnjom proizvodnjom, velikom složenošću i strogim tehničkim zahtjevima. Godišnji obim proizvodnje i godišnja tonaža ovih proizvoda su veoma visoki. Kompleksne su veličine, zahtjevni za metalografsku strukturu i imaju tendenciju stvaranja šupljina za skupljanje. Ovi proizvodi ne smiju imati nikakav rizik kvalitete, u protivnom će gubitak biti vrlo ozbiljan.
Strogi zahtjevi u pogledu performansi bloka motora, glave motora i sjedišta cilindra postavili su temelj za specifikacije proizvodnih proizvoda. Kako bi se postigle najbolje sveobuhvatne performanse lijevanja, obradivosti i mehaničkih svojstava, stopa sferoidizacije trebala bi biti u rasponu od 0% do 20% u svim ključnim dijelovima komponente. Što je još važnije, grafit se mora apsolutno izbjegavati kako bi se spriječilo oštećenje dijelova uzrokovano lokalnom slabošću. Kako bi se postigla dobra mehanička aditivnost, slobodni karbidi moraju se smanjiti na minimum. Zbog toga se titanijum nikada ne smije dodavati. Konačno, sa proizvodnog gledišta, ljevaonici je potreban stabilan i pouzdan proces kako bi se osigurala najniža stopa otpada uzrokovana metalografskom strukturom. Proizvođači u automobilskoj industriji zahtijevaju osiguranje kvalitete, a 100% odljevaka mora zadovoljiti metalografske zahtjeve. Opsežna, pouzdana proizvodnja blokova cilindara, glava cilindra i sjedišta cilindra zahtijeva preciznu analizu i internetsko podešavanje rastopljenog željeza kako bi se uklonile fluktuacije u procesu prije izlijevanja.
Stabilnost vermikularnog gvožđa
Razlog zašto se zbijeno željezo ne koristi u velikim količinama za proizvodnju složenih dijelova (poput blokova motora) je zato što je stabilna površina zbijenog željeza premala da bi se osiguralo da nema rizika u proizvodnji. Općenito govoreći, ova stabilna zona obuhvaća samo područje od 0.008% magnezija, kao što je prikazano na slici 2. Veličina i položaj platforme u stabilnoj zoni variraju ovisno o proizvodu. Zapravo, raspon magnezija je manji od ovoga. Budući da će svakih 5 minuta aktivni magnezij sagorijevati 0.001%. Početna tačka tečenja rastaljenog gvožđa mora biti dovoljno udaljena od oštre tačke skretanja zbijenog gvožđa do sivog gvožđa kako bi se osiguralo da se u završnom livenom delu ne pojavi ljuspasti grafit. Kada se u rastopljeno gvožđe doda magnezijum, pahuljica grafit će se pojaviti za oko 15 minuta.
Početna točka ne smije biti previše blizu desne strane stabilne platforme (visok sadržaj magnezija), jer će u protivnom uzrokovati stvaranje velike količine sferoidnog grafita u tanjem dijelu i dijelu za brzo hlađenje.
Osim male raspoložive površine platforme, površina platforme se uvijek kreće. Ako je sadržaj aktivnog kisika i sumpora visok, oni će trošiti aktivniji magnezij i cijela platforma će se pomaknuti udesno (visok sadržaj magnezija). Nasuprot tome, ako je sadržaj aktivnog kisika i sumpora nizak, platforma će se pomaknuti ulijevo (nizak sadržaj magnezija). Promjene u sastavu sirovina, čistoći, stepenu oksidacije i vlažnosti itd. Onemogućuju ljudima kontrolu vermikularnog gvožđa sa fiksnim rasponom hemijskog sastava.
Iako konverzijom iz vermikularnog željeza u sivo željezo treba samo smanjiti aktivni magnezij za 0.001%, sagorijevanje magnezija ne uzrokuje da cijeli dio postane ljuskasti grafit. Kada aktivni magnezij nije dovoljan, grafit prvo formira pahuljice i širi se prema van pri učvršćivanju, a magnezij se spušta i koncentrira na prednjem kraju sučelje kruta-tekućina. Ako je početna količina aktivnog magnezija odgovarajuća, vermikularni grafit će se formirati na granici eutektike, kao što je prikazano na slici 3. Grafit u ljusci se prvi put pojavljuje kao raspršene ljuspice. Za razliku od svih uobičajenih grafitnih ljuspica, ove izolirane ljuskaste grafitne mrlje teško je otkriti ultrazvukom. Vjerojatnost njihovog skeniranja ultrazvukom nije velika.
Osetljivost magnezijuma na vermikularno gvožđe može se prikazati na slici 4: U tonu vrelog metalnog lonca dodajte samo 10 grama magnezijuma, mrlje grafitne mrlje raspršene u uzorku Φ25 mogu se potpuno pretvoriti u vermikularni grafit. Vlačna čvrstoća ispitne šipke s mrljastim grafitnim mrljama iznosi samo 300 MPa, dok vlačna čvrstoća iste ispitne šipke s potpunim puzanjem doseže 450 MPa.
Inokulant je također vrlo osjetljiv na stabilnu platformu vermikularnog gvožđa, kao što je prikazano na slici 5: dodavanjem 80 grama inokulanta na jednu tonu rastopljenog gvožđa povećaće se stopa sferoidizacije u ispitnoj traci Φ25 sa 3% na 21%. Količina inokulacije je velika, a jezgra kristala je velika, što pogoduje stvaranju sfernog grafita. Ovo podiže vermikularnu željeznu platformu u smjeru velike stope sferoidizacije. Niska stopa inokulacije uzrokuje pomicanje platforme prema dolje. Brojni faktori, poput temperature pregrijavanja rastaljenog gvožđa, vremena zadržavanja, hemijskog sastava sirovina, vrste inokulanta i količine inokulacije, uticati će na položaj vermikularne gvozdene platforme.
Najosnovniji zahtjev bilo koje tehnologije upravljanja procesima je precizno mjerenje i analiza stanja rastaljenog gvožđa. Za vermikularno gvožđe pouzdana kontrola proizvodnje zahtijeva istovremeno mjerenje kritične tačke aktivnog magnezijuma iz tranzicije puzanja u pepeo, stepen naknadnog sagorijevanja magnezijuma i stepen inokulacije.
Uzorak termičke analize od 200 grama dobiva se umetanjem Xinte sonde u rastopljeno željezo nakon sferoidizacije i inokulacije. Tokom procesa umetanja od tri sekunde, zid sonde i rastopljeno gvožđe dostižu stanje toplotne ravnoteže. Za razliku od konvencionalne termalne čaše za uzorkovanje, ovaj uzorkivač sa tankim stijenkama ne samo da svaki put jamči isti volumen uzorka, već i izbjegava oksidaciju u rastopljenom željezu koje se ulijeva u čašu za uzorak. Mjerenje pregrijavanja je preciznije jer ne postoji fenomen kao što je pojava nasilne kondenzacije u konvencionalnoj termičkoj analizi.
Kao što je prikazano na slici 6a, Xinte sonda je izrađena od prešanog rastegnutog čeličnog lima. To je u osnovi sferni spremnik. Tanka čelična stijenka koja sadrži rastopljeno željezo ima izolacijski sloj nalik vakuumskoj tikvici. Debljina izolacijskog sloja simetrično se zadebljava prema smjeru visine kako bi se osiguralo ravnomjerno rasipanje topline i hlađenje u okolinu, a željezna zz voda u njemu blizu je skrućivanja sfernog tijela. U zaštitnoj cijevi u sondi postoje dva termoelementa tipa N. Termoelement se može izvući nakon svakog mjerenja i koristiti više puta više od 100 puta. Jedan od dva termoelementa nalazi se na dnu kontejnera, a drugi se nalazi u termalnom središtu spremnika. Budući da je spremnik sferičan i slobodno ovješen (to se razlikuje od konvencionalne čaše za uzorke termičke analize koja leži na konzoli koja apsorbira toplinu), rastopljeno željezo stvara ujednačen protok topline u spremniku, kao što je prikazano na slici 6b. Ovaj tok topline uzrokuje stalnu izmjenu rastopljenog željeza u spremniku, formirajući protočnu pregradu na dnu sonde.
Kako bi se imitirao prirodni gubitak rastopljenog gvožđa tokom izlivanja, na zidu sonde nalazi se premaz koji reaguje sa aktivnim magnezijumom. Rastopljeno gvožđe teče duž obloženog zida pokrenuto strujanjem toplote. Nakon reakcije, sadržaj magnezija u rastopljenom željezu se smanjuje i nakuplja u odjeljku na dnu spremnika. Direktno govoreći: Termopar u središtu sonde mjeri nereagirano rastopljeno željezo, koje je početno stanje izlijevanja; termoelement na dnu mjeri stanje nakon završetka izlijevanja. Formulacija reaktivnog premaza je vrlo specifična. Mora se točno osigurati da je rastopljeno željezo nagomilano u odjeljku 0.003% manje aktivno od središnjeg rastaljenog željeza. Stoga, ako je početni sadržaj magnezija preblizu tački okretanja puzanja, rastopljeno gvožđe u odjeljku će generirati sivo željezo, što će se mjeriti termoelementom u ovoj oblasti. Na ovaj način, na početku lijevanja, radionica može dodati još magnezija kako bi nadoknadila neizbježan gubitak sagorijevanja magnezija.
Ako termopar na dnu pokazuje vermikularnu željeznu krivulju, to znači da je početni sadržaj magnezija dovoljno visok da nakon završetka lijevanja neće biti ljuskavog grafita.
Slika 7 je dijagram erozije presjeka Xinte sonde nakon mjerenja uzorka. Na slici možete jasno vidjeti pregradno područje, područje glavnog uzorka i zaštitnu cijev termopara. Kako se aktivni magnezij smanjuje za 0.003%, u zoni odvajanja nastaju grafitna i feritna matrica u obliku slova D. Veličina ljuskastog grafita na dnu direktno odražava početni sadržaj magnezija u području glavnog uzorka. Veličina ove zone može se izračunati iz topline koja se oslobađa na dnu. Koeficijent regresije varijance između oslobađanja topline i veličine pregrade prelazi 0.9, što dokazuje da je odnos između njih vrlo blizak. Oslobođena toplota se dobija integracijom vremenske krive hlađenja. Ova metoda mjerenja stanja rastopljenog željeza u trenutku i na kraju izlijevanja osigurava točnost sadržaja magnezija prije ulijevanja.
Budući da je vermikularno željezo vrlo osjetljivo na sferoidizirajuća sredstva i inokulante, za ljevaonice je nemoguće koristiti prekomjerne metode obrade koje se koriste u proizvodnji sivog i nodularnog liva. Kao što je prikazano na slici 8, vermikularno željezo je zbog svoje osjetljivosti stabilno samo unutar kvadratnog prozora, a ne samo u području magnezijeve platforme. Pouzdan proces proizvodnje vermikularnog željeza mora kontrolirati sferoidizaciju i inokulaciju od početka do kraja kako bi se osiguralo da metalografska struktura ispuni cilj.
Bez obzira koliko se truda uložilo, koliko god se strogo upravljalo, fluktuacija rastaljenog gvožđa uvijek je neizbježna. A kamoli koliko ljudi znaju o tretmanu rastaljenog gvožđa, metode obrade u jednom koraku, poput sendvič metode, ne mogu garantovati da će svaki tretman pasti unutar uskog vermikularnog gvozdenog prozora. Brojne proizvodne varijable, kao što su omjer miješanja, temperatura peći, vrijeme držanja, stupanj predgrijavanja kutlače rastopljenog željeza, brzina točenja, položaj točenja točenja željeza (unutar ili izvan mjerenja), težina rastopljenog željeza, stanje vrećice od legure, sferoidizirajuće sredstvo stvarni sadržaj magnezijuma (PeSiMg), raspored legura svakog sloja u sendvič metodi i pokrivenost otpacima od željeznog otpada, itd., sve će utjecati na apsorpciju magnezija. Osim ovih faktora, sadržaj aktivnog kisika i aktivnog sumpora također će promijeniti veličinu i položaj vermikularnog željeznog prozora. Promjene vremena zadržavanja istopljenog gvožđa u kašici, vremena transporta i vremena sipanja promijeniće raspoloživo vrijeme gorenja.
Međutim, najnepredvidljiviji faktori fluktuacije su greške operatora ili razlike između različitih operatera zbog različitih radnih navika.
U masovnoj proizvodnji velikih razmjera, jedini siguran način je mjerenje karakteristika očvršćavanja rastaljenog gvožđa nakon tretmana. Na ovaj način, različiti faktori koji utječu na veličinu, položaj i apsorpciju legure prozora od vermikularnog željeza sveobuhvatno su izmjereni, analizirani i uzeti u obzir. Tada se može dodati odgovarajuća količina magnezija i inokulanta. Svaki lonac rastopljenog gvožđa sipa se nakon što je nadograđen u idealno stanje. Ova metoda upravljanja postupkom mjerenja i podešavanja u dva koraka minimizira varijabilnost proizvodnje i potpuno eliminira rizik od ljuspanja grafita u lijevanju.
Kontrola procesa proizvodnje vermikularnog gvožđa sa kutlačom od vrućeg metala
Kao što je prikazano na slici 9, kontrola procesa započinje termičkom analizom rastopljenog željeza nakon početne obrade sferoidizacijom i inokulacijom. Prema rezultatima analize, mašina za uvlačenje žice automatski prikazuje dužinu žice koju treba dodati magnezijumom i inokulantom i čeka da je operater pokrene. Kad se dovodna linija završi, kutlača se odmah šalje na liniju za lijevanje. Cijeli proces mjerenja i podešavanja traje oko tri minute. U tom razdoblju radionica može izvesti uobičajene tretmane predlijevanja, poput uklanjanja troske. Ovo osigurava kontinuitet linije za lijevanje.
S operativne tačke gledišta, sirovo rastopljeno željezo ne sadrži magnezij, a kapacitet inkubacije je također vrlo ograničen. Nakon sferoidizacije i inokulacije, magnezij i inokulanti prvo pojedu aktivni kisik i sumpor u rastopljenom željezu, a zatim "skoče" rastopljeno željezo u određeni položaj na ploči. U primjeru na slici 10, indeks magnezijuma i indeks inokulacije rastaljenog gvožđa su 65, odnosno 45. Budući da su glavni parametri promjene proizvodnje sjene prikazani u rastopljenom željezu nakon mjerenja i obrade, rezultati termičke analize direktno odražavaju trenutno stanje rastopljenog željeza. Ostaje samo dodati odgovarajuću količinu magnezija i inokulanta da se rastaljeno gvožđe podigne sa trenutnog položaja na željenu početnu tačku. U primjeru na slici 10, prvo se dodaje sedam jedinica magnezijevih kabela, a zatim se dodaje 23 jedinice kabela za inokulaciju. Odgovarajući odnos između jedinice indeksa i dužine kabela kalibrira se u skladu s proizvodom i radionicom i sastavlja se u programu. Na osnovu dosadašnjeg iskustva s gotovo 100,000 vermikularnih odljevaka od željeza, prosječna količina magnezijevog kabela dodana je 5 metara po toni. Sadrži 12 grama magnezija po metru, a računato pri stopi apsorpcije od 50%, količina magnezija dodanog po toni rastopljenog željeza iznosi samo 30 grama. Budući da je količina dodatka vrlo mala, a glavne promjene su se već dogodile u početnom tretmanu, prilagodba je vrlo učinkovita i pouzdana. Nakon podešavanja nema potrebe za termičkom analizom.
U početnom tretmanu stanje nakon tretmana treba biti niže od početnog položaja izlijevanja, tako da čak i ako svi faktori koji su korisni za apsorpciju magnezija i inokulanta dostignu optimalnu vrijednost, rastopljeno željezo će doseći samo početno stanje lijevanja . Osim ako se ne pretjeruje, rastopljeno željezo nakon tretmana nije u stanju sivog i bijelog željeza. Kako bi proces lijevanja bio efikasniji, indeks magnezijuma i indeks inokulacije svake kašike istopljenog gvožđa prikazani su u blok dijagramu procesa. U skladu s promjenjivim trendom blok dijagrama, operater može prilagoditi količinu rastopljenog željeza dodanog u sljedeću kašiku. Vrijednost ekvivalenta ugljika također se prikazuje na ekranu. Ti su podaci uređeni i pohranjeni u dnevnik proizvodnje, tako da im se može pratiti i obuhvatiti ih, a ispunjavaju i zahtjeve osiguranja kvalitete.
Iako termička analiza i naknadna prilagođavanja mogu osigurati proizvodnju vermikularnog željeza, preporučuje se uzimanje uzoraka iz šalice sprua posljednjeg lijevanja za analizu. U usporedbi s konvencionalnom kontrolom kvalitete, ovaj rezultat termičke analize može pružiti internetsku analizu i klasificirati odljevke ako je potrebno. Simulacija gubitka magnezija u sondi čini ovu "nedestruktivnu" tehniku pregleda učinkovitijom od metalografskih i ultrazvučnih metoda. Budući da ova metoda mjeri veću veličinu uzorka, ona također detektira kako će se rastopljeno željezo očvrsnuti u sljedećih 10-15 minuta.
Da sumiram
Izbor sistema upravljanja procesom ovisi o proizvodu i procesu lijevanja. Prilikom lijevanja složenih proizvoda, poput poklopca motora i cilindra od vermikularnog željeza, sistem mora istovremeno kontrolirati sadržaj magnezija i inokulanta, tako da se nalazi u vrlo uskom prozoru od početka do kraja ulijevanja. Stopa sferoidizacije mora biti između 0% i 20% (stopa puzanja 80% do 100%) kako bi se osigurala najbolja sposobnost lijevanja, mehanička aditivnost i druge sveobuhvatne performanse i najbolja upotrebna funkcija. Mrlje od grafita moraju se potpuno ukloniti kako bi se spriječile lokalne greške i slabosti.
Polazna tačka svakog sistema za upravljanje procesima je precizno i efikasno mjerenje stanja rastopljenog gvožđa. Pouzdana velika proizvodnja vermikularnog željeza mora imati izvodljive metode kontrole kako bi se uklonile promjene procesa i greške u ljudskom radu. Najefikasniji način za uklanjanje promjena procesa je provođenje termičke analize na rastopljenom željezu nakon sferoidizacije i inokulacije. Prema rezultatima termičke analize, prije izlijevanja dodatno se dodaje točna količina magnezija i inokulanta. Ova mrežna metoda mjerenja i podešavanja osigurava stabilnost proizvodne linije za lijevanje i uklanja različite rizike koje donosi proizvodnja velike količine vermikularnog željeza.
Molimo zadržite izvor i adresu ovog članka radi ponovnog štampanja: Kontrola procesa proizvodnje vermikularnog željeza
Minghe Tvrtka za lijevanje tla posvećeni su proizvodnji i pružaju kvalitetne dijelove i dijelove za lijevanje visokih performansi (opseg dijelova za livenje metala uglavnom uključuje Tankozidno lijevanje,Vruće komore Die Casting,Livenje u hladnoj komori), Okrugla usluga (usluga lijevanja,CNC obrada,Izrada kalupa, Površinska obrada). Bilo koji prilagođeni lijev od aluminija, livenje magnezijumom ili Zamakom / cinkom i drugi odljevci dobrodošli su da nas kontaktirate.
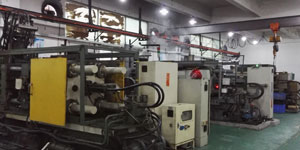
Pod kontrolom ISO9001 i TS 16949, svi procesi se provode kroz stotine naprednih mašina za livenje pod tlakom, 5-osnih mašina i drugih objekata, od blastera do Ultra Sonic mašina za pranje rublja. Minghe ne samo da ima naprednu opremu već ima i profesionalnu opremu tim iskusnih inženjera, rukovatelja i inspektora kako bi ostvarili dizajn kupca.
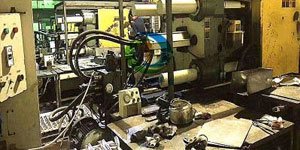
Ugovorni proizvođač kalupa. Mogućnosti uključuju dijelove za livenje aluminijuma u hladnoj komori od 0.15 lbs. do 6 lbs., brza promjena i obrada. Usluge s dodanom vrijednošću uključuju poliranje, vibriranje, uklanjanje brušenja, miniranje sačmama, farbanje, oblaganje, premazivanje, montaža i obrada alata. Materijali s kojima se radi uključuju legure poput 360, 380, 383 i 413.
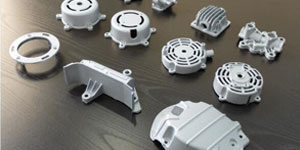
Pomoć pri dizajniranju lijevanja cinkom / istovremene inženjerske usluge. Prilagođeni proizvođač preciznih odljevaka od cinka. Mogu se proizvoditi minijaturni odljevci, odljevci za kalupe pod visokim pritiskom, odlivci kalupa sa više klizača, konvencionalni odljevci od kalupa, odljevci za kalupe i neovisni kalupi i odljevci sa šupljinom. Odljevci se mogu izrađivati u dužinama i širinama do 24 in. U toleranciji +/- 0.0005 in.
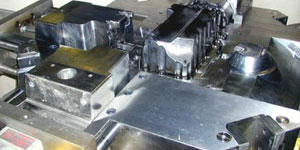
ISO 9001: 2015 certificirani proizvođač lijevanog magnezijuma. Mogućnosti uključuju lijevanje magnezijumom pod visokim pritiskom do 200 tona vruće komore i 3000 tona hladne komore, dizajn alata, poliranje, oblikovanje, obrada, farbanje u prahu i tečnostima, puni QA sa CMM mogućnostima , montaža, pakovanje i dostava.
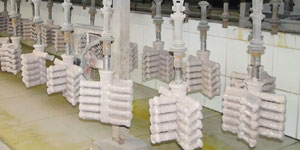
Ovjeren ITAF16949 Dodatna usluga lijevanja uključuje investiranje,livenje peska,Gravitacijsko lijevanje, Casting Lost Foam,Centrifugalno livenje,Vakuumski livenje,Trajno lijevanje kalupa, .Sposobnosti uključuju EDI, inženjersku pomoć, solidno modeliranje i sekundarnu obradu.
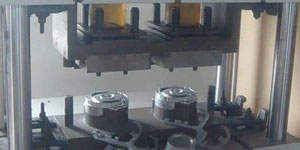
Casting Industries Studije slučaja za dijelove za automobile, bicikle, zrakoplove, muzičke instrumente, plovila, optičke uređaje, senzore, modele, elektroničke uređaje, kućišta, satove, mašine, motore, namještaj, nakit, vrpce, telekom, osvjetljenje, medicinske uređaje, fotografske uređaje, Roboti, skulpture, zvučna oprema, sportska oprema, alat, igračke i još mnogo toga.
Šta vam možemo dalje pomoći?
∇ Idite na početnu stranicu za Kina za lijevanje pod pritiskom
→Dijelovi za lijevanje- Otkrij šta smo uradili.
→ Povezani savjeti o Usluge lijevanja
By Proizvođač lijevanja Minghe | Kategorije: Korisni članci |materijal Tagovi: Aluminijsko livenje, Lijevanje cinka, Magnezijum lijevanje, Titanijsko livenje, Lijevanje nehrđajućeg čelika, Lijevanje od mesinga,Lijevanje bronce,Casting Video,Istorija kompanije,Aluminijsko livenje | Komentari isključeni