Kontrola atmosfere tokom procesa sinterovanja sinteriranog čelika i njegove performanse
Atmosfera sinterovanja i njen izbor
Ako se uzme u obzir samo sinteriranje čelika koji sadrži ugljik, atmosfera za sinterovanje koja se koristi u industriji metalurgije praha je vodik, dušik, dušik + vodik (potencijal ugljika ili bez ugljika), razgradnja amonijaka, endotermni plin, endotermni plin + dušik, sinteza Za gas i vakuum, ispravan izbor atmosfere za sinterovanje zahteva razumevanje karakteristika i performansi različitih atmosfera za sinterovanje, i odabir u skladu sa principima obezbeđivanja kvaliteta i smanjenja troškova.
Vodik je snažna redukcijska atmosfera. Mnogi ljudi vjeruju da vodik ima određeni učinak dekarburizacije, ali to uvelike ovisi o čistoći korištenog vodika, a ne o samom vodiku. Općenito, vodik nakon elektrolize ili katalitičke konverzije sadrži određenu količinu nečistoće, poput H2O, O2, CO i CH4, itd., Ponekad ukupna količina može doseći oko 0.5%. Stoga je najbolje osušiti i očistiti prije upotrebe kako bi se smanjio sadržaj kisika i tačka rosišta. Međutim, zbog visoke cijene vodika, čisti vodik rijetko se koristi kao atmosfera za sinteriranje, osim ako za to postoje posebni razlozi.
Dušik je siguran i jeftin inertni plin, ali budući da čisti dušik nema mogućnost reduciranja na temperaturi sinteriranja, čisti se dušik rijetko koristi kao atmosfera za sinteriranje u proizvodnji tradicionalnog metala u prahu. Posljednjih godina, kako su se smanjili troškovi pročišćavanja dušika i poboljšala hermetičnost peći za sinteriranje, dušik se također počeo koristiti kao atmosfera za sinteriranje za sinteriranje čelika koji sadrži ugljik.
Posljednjih se godina mješavina dušik-vodik sve više koristi za sinterovanje ugljičnog čelika. Dušik/vodik obično se koristi između 95/5-50/50. Ova mješavina ima određeni stupanj reduciranosti i točka rosišta može doseći Ispod -60 ℃, općenito govoreći, mora se dodati određena količina CH4 ili C3H8 kako bi se održao određeni potencijal ugljika pri korištenju ovog plina na 1050-1150 ℃, dok se sinterira ugljični čelik iznad 1250 ℃ ne mora kontrolirati potencijal ugljika. Ova smjesa se može koristiti za sinteriranje legura na bazi željeza na bazi kroma ispod 1120 ° C bez oksidacije.
Razloženi amonijak nastaje razlaganjem amonijačnog plina kroz zagrijani katalizator, uključujući 75% H2 i 25% N2. Ali općenito govoreći, mala količina neraspadnutih molekula amonijaka uvijek ostaje u raspadnutom amonijaku. Kada su u kontaktu s vrućim metalom na visokim temperaturama, oni će se razgraditi na visoko aktivne atome vodika i dušika, čime se metal nitrira. Nedavna istraživanja pokazala su da će se, ako se pravilno kontrolira, sinteriranje AstaloyCrM na 1120 ° C razgraditi i amonizirati smjesu 90N2/10H2 sa jačom redukcijom. Glavni razlog je taj što su ti aktivni atomi vodika koji su upravo razloženi tijekom procesa sinteriranja učinkovitiji od 90N2/ Vodik u 10H2 miješanom plinu ima jaču reduciranost i može učinkovito smanjiti oksidni sloj izvan čestica AstaloyCrM. Za pročišćavanje i razgradnju amonijaka, možete ga propustiti kroz vodu i osušiti, ili upotrijebiti aktivirani glinica ili molekularno sito za uklanjanje preostalog. Sav amonijak se uklanja.
Endotermni plin je vrsta miješanog plina koji se dobiva miješanjem ugljikovodičnog plina (CH4 ili C3H8) sa zrakom u određenom omjeru, prethodno zagrijavanjem na 900-1000 ° C i katalitičkom konverzijom pomoću katalizatora niklovog oksida. Ovisno o omjeru zraka i plina ugljena, proces pretvorbe prati endotermna ili egzotermna reakcija. Rezultirajući miješani plin naziva se endotermni plin ili egzotermni plin, a reakcija može biti sljedeća:
CmHn+m(O2+3.774N2)—mCO+n/H2+1.887mN2
Ako se gornja reakcija mora provesti u potpunosti, to jest, sav C u CmHm je upravo reagirao s O2 u zraku, potreban zrak/plin trebao bi biti m/2 (1+3.774), što je 2.387 m. Na primjer, ako se koristi ugljikovodični plin CH4, potreban zrak/plin trebao bi biti 2.387, a miješani plin koji se proizvodi u ovom trenutku uključuje 40.9% H2, 38.6% N2 i 20.5% CO. Nakon reakcije, miješani plin sadrži H2 Sadržaj CO i CO opada s povećanjem zraka/plina, ali se povećava sadržaj H2O i CO2. Također pokazuje da se potencijal ugljika u miješanom plinu nakon reakcije smanjuje s povećanjem zraka/plina, a performanse oksidacije se povećavaju. Ovo je ujedno i glavni razlog zašto se egzotermni plin rijetko koristi pri sinteriranju čelika koji sadrži ugljik, a koristi se većina endotermnih plinova.
Općenito govoreći, miješani plin proizveden zrakom/plinom između 2.0-3.0 naziva se apsorpcijski vrući plin, a miješani plin proizveden kada je omjer veći od 5.0 naziva se egzotermni plin. Odnos između točke rosišta endotermnog plina proizvedenog s CH4 kao sirovinom i zraka/plina pokazuje da zrak/plin raste samo sa 2.4 na 2.5, a točka rosišta proizvedenog miješanog plina raste s -25 ° C na iznad 0 ° C. Stoga, ako korisnici sami proizvode endotermni plin, trebali bi obratiti posebnu pažnju na kontrolu omjera zraka i plina u sirovinama (po mogućnosti ne više od 2.4) kako bi dobili endotermni plin s dovoljno niskom rosištem. U miješanom plinu nakon reakcije, omjer različitih plinova odgovara omjeru na kraju reakcije, koji je općenito (1000-1100 ° C).
Nakon reakcije, ako se temperatura plina promijeni, promijenit će se potencijal ugljika miješanog plina, tačka rosišta i omjer različitih plinova. Mnogi proizvođači metalurgije praha koriste jedan egzotermni generator plina za opskrbu potrebne atmosfere za sinteriranje za nekoliko peći za sinteriranje istovremeno kroz cjevovod. Temperatura atmosfere je snižena prije nego što je stigla do peći za sinteriranje. . Ako izolacija cjevovoda nije dobra, a temperatura zida cjevovoda niža od 800 ° C, tada će se dio ugljika u mješovitom plinu odložiti na stijenku cjevovoda u obliku čađe. Drugim riječima, kada se miješani plin ponovo zagrije na temperaturu sinterovanja u peći za sinteriranje, njegova je ugljična toplina mnogo niža od potencijala ugljika koji može dati endotermni generator plina.
U tom slučaju, u peć za sinteriranje treba dodati odgovarajuću količinu metana ili propana kako bi se osigurao potencijal ugljika u peći. Sada su neki strani proizvođači metalurgije praha počeli instalirati mali endotermni generator plina pored svake peći za sinteriranje i koristiti endotermni plin koji je upravo proizveden izravno u peć za sinteriranje bez hlađenja, kako bi se izbjeglo utjecaj na atmosferu sinteriranja zbog temperaturnih promjena . . Još jednu stvar koju treba podsjetiti je da čak i uz katalitičko djelovanje katalizatora nikl -oksida, mala količina ugljikovodičnog plina (CH4 ili C3H8, itd.) Ostaje u miješanom plinu dobivenom nakon transporta. Osim toga, između plinova na 900-1100 ℃ Nakon što reakcija postigne ravnotežu, proizvest će se mala količina CO2 i H2O (plinovita), koje je potrebno osušiti prije upotrebe.
Dodavanjem dušika endotermnom plinu može se smanjiti relativni sadržaj CO, CO2 i H2O u endotermnom plinu, tako da se umanji osjetljivost atmosfere na potencijal ugljika i tačku rose, te olakšaju neki koeficijenti korelacije u atmosferi sinteriranja kontroli.
Sintetički plin je metoda koju su posljednjih godina predložili strani proizvođači peći za sinteriranje za izravno generiranje (razrjeđivanje) endotermnog plina u peći za sinteriranje (bez potrebe za endotermnim generatorom plina izvan peći). On miješa plinoviti metil alkohol i dušik u određenom omjeru, a zatim ga izravno prenosi u peć za sinteriranje. Sljedeće reakcije će se dogoditi u zoni sinteriranja na visokoj temperaturi:
CH3OH — CO+2H2
Budući da je omjer CO i H2 u raspadnutom plinu jednak omjeru endotermnog plina proizvedenog uobičajenom metodom sa CH4, a miješani dušik može se kombinirati kako bi se sintetizirala miješana atmosfera istog sastava kao i endotermni plin (1L Metan odgovara 1.05 nm3 dušika). Njegova najveća prednost je ta što ne zahtijeva endotermni generator plina izvan peći. Osim toga, korisnici mogu miješati različite količine dušikovog plina kako bi proizveli razrijeđeni endotermni plin prema vlastitim potrebama.
Vakuum je također vrsta atmosfere za sinteriranje, koja se uglavnom koristi za sinteriranje nehrđajućeg čelika i drugih materijala, ali se obično ne koristi za sinteriranje ugljičnog čelika.
Fizička svojstva atmosfere za sinteriranje
Većina radova i izvještaja o atmosferi sinteriranja uglavnom raspravlja o kemijskom ponašanju između različitih atmosfera sinteriranja i sinteriranog tijela tijekom procesa sinteriranja, ali rijetko raspravlja o utjecaju fizičkih svojstava različitih atmosfera na sinteriranje, iako je taj učinak u mnogim slučajevima nemoguć. biti zanemaren. Na primjer, razlika u viskoznosti plina uzrokovat će kemijski gradijent koncentracije sinteriranog tijela od površine prema unutra duž otvora, čime će utjecati na površinska svojstva sinteriranog tijela. Na primjer, toplinski kapacitet i toplinska vodljivost različitih plinova imaju veliki utjecaj na vrijeme sinterovanja i brzinu hlađenja. Ovaj odjeljak navodi glavna fizička svojstva nekih atmosfera za sinteriranje na različitim temperaturama (oko temperature sinterovanja) za referencu čitatelja.
Primjeri problema vezanih za atmosferu tokom sinterovanja
1 Primjeri pucanja na površini dijelova tijekom deparafiranja
Kada se koristi peć za sinteriranje s mrežicom i endotermni plin se koristi kao atmosfera za sinteriranje, ako brzina porasta temperature i atmosfera u zoni deparafiranja nisu dobro kontrolirani, doći će do površinskog pucanja. Mnogi ljudi misle da je ova pojava posljedica brzog raspadanja maziva koja je uzrokovana, ali to nije slučaj. Pravi razlog je taj što se ugljikov monoksid u endotermnom plinu razgrađuje u čvrsti ugljik i ugljikov dioksid u temperaturnom rasponu od 450-700 ℃ pod katalizom željeza, nikla i drugih metala. Novo taloženi čvrsti ugljik u porama sinteriranog tijela povećava njegov volumen i uzrokuje gore spomenuti fenomen površinskog pucanja.
Kvaliteta dijelova varira ovisno o temperaturi tijekom procesa sinteriranja u različitim atmosferama. Među njima, atmosfera 3 je suhi endotermni plin ugljena, a atmosfere 4 i 5 su endotermni plin ugljena dodane s različitim količinama vodene pare. Može se vidjeti da tijekom procesa sinteriranja kvaliteta dijelova počinje opadati na oko 200 ° C, što znači da se kruto mazivo unutar njega kontinuirano razgrađuje i prelijeva tijelo za sinteriranje, smanjujući njegovu kvalitetu. Naravno, ako u miješanom prahu nema čvrstog maziva, gornji fenomen ne postoji. Ako se koriste gornje tri atmosfere, što je atmosfera suša od kvalitete sinteriranog tijela na oko 450 ° C, to će ovaj fenomen biti ozbiljniji.
Ali ono što je zanimljivo je da se pri upotrebi plina 3 (suhi endotermni plin) dolazi do površinskog pucanja bez obzira na prisutnost čvrstih maziva, što ukazuje da nije izravno povezano s deparafiranjem, a u pukotinama se nalazi plin bogat ugljikom. Fenomen, možemo potvrditi tačnost gornjeg objašnjenja.
Postoji nekoliko načina da se izbjegne pojava gore spomenute pojave pucanja. Najdirektnije je promijeniti atmosferu sinterovanja iz endotermnog plina u smjesu vodik-dušik bez pucanja prekinutih linija. Ako se atmosfera za sinteriranje ne može promijeniti, postoje dvije metode. Jedan je upuhivanje dijela endotermnog plina koji sadrži vodenu paru u zonu za deparafiranje peći za sinteriranje. Međutim, ovom metodom je teško postići stabilnu kontrolu u stvarnom radu.
Kontrola protoka zraka u peći za sinteriranje nije dobra, a pojava visoke atmosfere rosišta koja ulazi u zonu sinteriranja može utjecati na kvalitetu sinteriranja. Druga i najbolja metoda je povećati brzinu zagrijavanja dijelova u zoni deparafiranja peći za sinteriranje kako bi što prije prošla 450. U području gdje dolazi do pucanja pri -600 ° C, za ovu pojavu obično je dizajnirano takozvano brzo uklanjanje voska.
2 Primjer sinteriranja AstaloyCrM
Metalni krom se široko koristi u legiranom čeliku zbog niske cijene i dobrog učinka jačanja. Međutim, sinterirani čelik koji sadrži krom naići će na mnoge probleme u svom proizvodnom procesu. Jedan je proizvodnja željeznog praha koji sadrži krom, koji mora proći strogu proceduru raspršivanja atomizacijom i žarenjem kako bi se dobio prah sirovine s nižim sadržajem kisika i ugljika. .
Švedska Honganas AB trenutno je jedini proizvođač na svijetu koji može proizvesti ovaj sirovinski prah po niskim cijenama. Drugi je da čak i ako se može dobiti visokokvalitetni željezni prah koji sadrži krom, ako se sinteriranjem i temperaturom medija, posebno atmosferom za sinteriranje, ne može dobro kontrolirati, veća je vjerojatnost da će oksidirati tijekom sinteriranja i oksidacije, a performanse sinterovanja će se smanjiti.
Termodinamički proračuni i veliki broj eksperimenata dokazali su da ako se endotermni plin koristi kao atmosfera za sinteriranje AsaloyCrM, zahtjevi za sinteriranjem ne mogu biti ispunjeni čak i ako je rosište vrlo nisko.
Drugim riječima, za sinteriranje AsaloyCrM-a može se koristiti samo čista smjesa vodika ili vodik-dušik. Trenutno se koristi većina potonjih. , Udio vodika iznosi 5%-20%. Čitatelja treba podsjetiti ne samo da osigura sastav atmosfere za sinteriranje, već i da osigura kvalitetu atmosfere za sinteriranje.
Takozvana kvaliteta ovdje se odnosi na stupanj oksidacije u atmosferi za sinteriranje, koji se općenito kalibrira parcijalnim pritiskom kisika u atmosferi. Prilikom sinterovanja na 1120 ℃, ako je parcijalni tlak kisika u atmosferi niži od 1 × 10-14Pa, do oksidacije neće doći tijekom procesa sinteriranja.
Kada se temperatura spusti, kako bi se spriječila oksidacija, potrebno je da parcijalni tlak kisika u atmosferi bude čak i nizak. Također se može osigurati da AsaloyCrM sinteriran na 1125 ℃ neće oksidirati pri 1 × 10-14Pa. Gornji izračun potvrđen je eksperimentalnim podacima.
Molimo zadržite izvor i adresu ovog članka radi ponovnog štampanja: Kontrola atmosfere tokom procesa sinterovanja sinteriranog čelika i njegove performanse
Minghe Tvrtka za lijevanje tla posvećeni su proizvodnji i pružaju kvalitetne dijelove i dijelove za lijevanje visokih performansi (opseg dijelova za livenje metala uglavnom uključuje Tankozidno lijevanje,Vruće komore Die Casting,Livenje u hladnoj komori), Okrugla usluga (usluga lijevanja,CNC obrada,Izrada kalupa, Površinska obrada). Bilo koji prilagođeni lijev od aluminija, livenje magnezijumom ili Zamakom / cinkom i drugi odljevci dobrodošli su da nas kontaktirate.
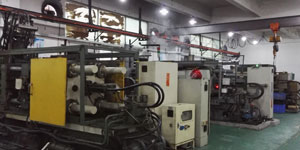
Pod kontrolom ISO9001 i TS 16949, svi procesi se provode kroz stotine naprednih mašina za livenje pod tlakom, 5-osnih mašina i drugih objekata, od blastera do Ultra Sonic mašina za pranje rublja. Minghe ne samo da ima naprednu opremu već ima i profesionalnu opremu tim iskusnih inženjera, rukovatelja i inspektora kako bi ostvarili dizajn kupca.
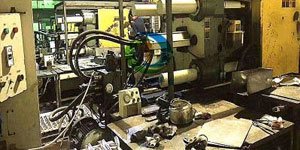
Ugovorni proizvođač kalupa. Mogućnosti uključuju dijelove za livenje aluminijuma u hladnoj komori od 0.15 lbs. do 6 lbs., brza promjena i obrada. Usluge s dodanom vrijednošću uključuju poliranje, vibriranje, uklanjanje brušenja, miniranje sačmama, farbanje, oblaganje, premazivanje, montaža i obrada alata. Materijali s kojima se radi uključuju legure poput 360, 380, 383 i 413.
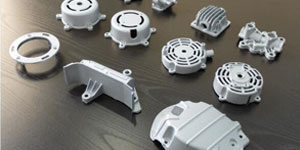
Pomoć pri dizajniranju lijevanja cinkom / istovremene inženjerske usluge. Prilagođeni proizvođač preciznih odljevaka od cinka. Mogu se proizvoditi minijaturni odljevci, odljevci za kalupe pod visokim pritiskom, odlivci kalupa sa više klizača, konvencionalni odljevci od kalupa, odljevci za kalupe i neovisni kalupi i odljevci sa šupljinom. Odljevci se mogu izrađivati u dužinama i širinama do 24 in. U toleranciji +/- 0.0005 in.
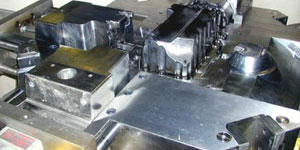
ISO 9001: 2015 certificirani proizvođač lijevanog magnezijuma. Mogućnosti uključuju lijevanje magnezijumom pod visokim pritiskom do 200 tona vruće komore i 3000 tona hladne komore, dizajn alata, poliranje, oblikovanje, obrada, farbanje u prahu i tečnostima, puni QA sa CMM mogućnostima , montaža, pakovanje i dostava.
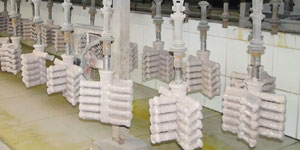
Ovjeren ITAF16949 Dodatna usluga lijevanja uključuje investiranje,livenje peska,Gravitacijsko lijevanje, Casting Lost Foam,Centrifugalno livenje,Vakuumski livenje,Trajno lijevanje kalupa, .Sposobnosti uključuju EDI, inženjersku pomoć, solidno modeliranje i sekundarnu obradu.
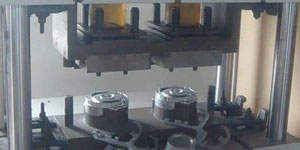
Casting Industries Studije slučaja za dijelove za automobile, bicikle, zrakoplove, muzičke instrumente, plovila, optičke uređaje, senzore, modele, elektroničke uređaje, kućišta, satove, mašine, motore, namještaj, nakit, vrpce, telekom, osvjetljenje, medicinske uređaje, fotografske uređaje, Roboti, skulpture, zvučna oprema, sportska oprema, alat, igračke i još mnogo toga.
Šta vam možemo dalje pomoći?
∇ Idite na početnu stranicu za Kina za lijevanje pod pritiskom
→Dijelovi za lijevanje- Otkrij šta smo uradili.
→ Povezani savjeti o Usluge lijevanja
By Proizvođač lijevanja Minghe | Kategorije: Korisni članci |materijal Tagovi: Aluminijsko livenje, Lijevanje cinka, Magnezijum lijevanje, Titanijsko livenje, Lijevanje nehrđajućeg čelika, Lijevanje od mesinga,Lijevanje bronce,Casting Video,Istorija kompanije,Aluminijsko livenje | Komentari isključeni